In the bustling environment of a heavy equipment dealership, the integration of the 5S methodology, especially in the context of service trucks, has shown to be a game-changer. 5S, a lean management tool, is not just a series of steps; it’s a culture that when ingrained, can significantly enhance the efficiency, safety, and overall performance of a dealership. Let’s dive into how this system can revolutionize your service trucks.
1. Sort
The first step, Sort, is about decluttering. Service trucks often become the repositories of tools and parts, some of which are rarely used. By identifying and keeping only essential items, technicians can reduce weight and improve the fuel efficiency of the trucks. This step is crucial in increasing the workspace efficiency and reducing potential safety hazards caused by unnecessary clutter.
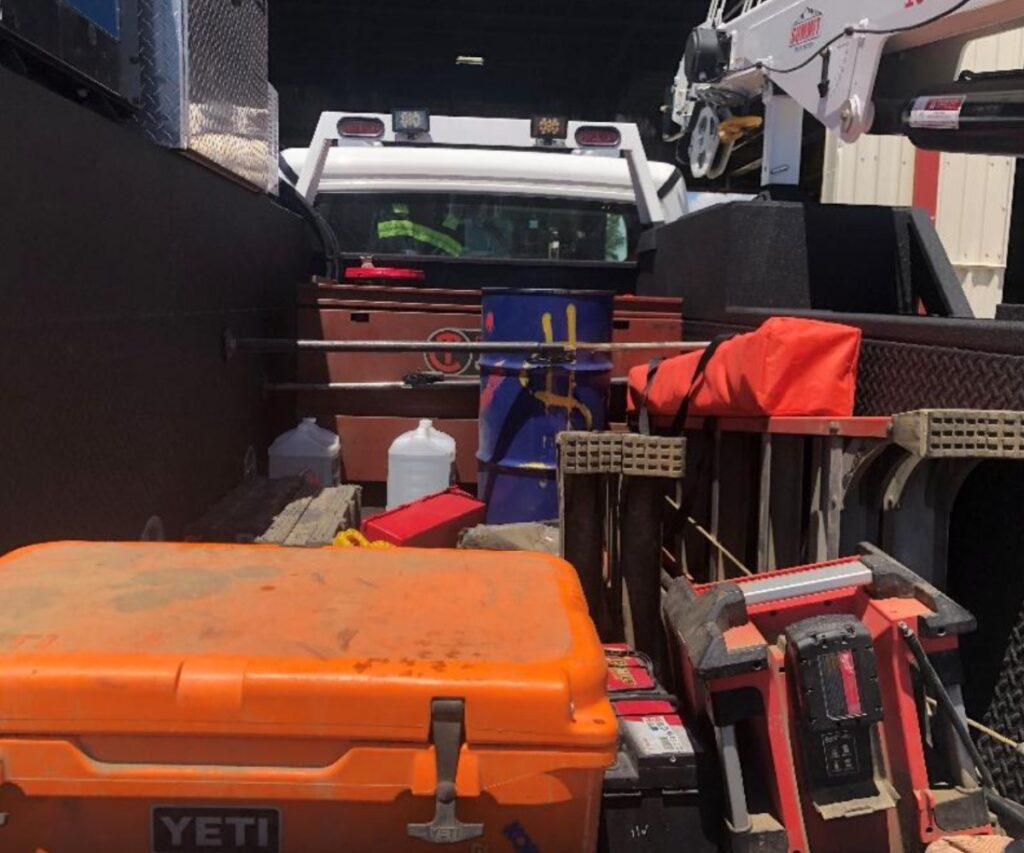
2. Set in Order
Once sorting is done, organizing the remaining items is key. Set in Order is all about finding a logical place for every tool and part. Customized foam tool trays, labeled bins, and digital inventory systems can be invaluable. This approach not only saves time during tool retrieval but also reduces the risk of leaving equipment behind at a job site. Moreover, it presents a professional image to customers, showing a well-organized and competent service.
3. Shine
Shine goes beyond mere cleaning. It’s about regular maintenance and inspection of the service trucks. Implementing a daily or weekly cleaning schedule ensures that the trucks are not just clean, but also in good working order. This step helps in identifying potential issues before they turn into costly repairs or cause downtime, ensuring reliability when servicing heavy equipment.
4. Standardize
Standardization is the key to consistency. Developing and implementing standard operating procedures (SOPs) for the maintenance and organization of service trucks ensures that the first three S’s are consistently applied. This can include checklists for truck loading and unloading, maintenance routines, and even the layout of tools and equipment. Standardization not only enhances efficiency but also makes it easier for different technicians to work interchangeably with minimal disruption.
5. Sustain
The final S, Sustain, is perhaps the most challenging yet the most crucial. It’s about building a culture where 5S principles are not just applied but lived daily. Regular training sessions, audits, and feedback mechanisms can help in sustaining these practices. It’s about creating a mindset among the team that values organization, efficiency, and continual improvement.
Final Thoughts
Incorporating 5S in the heavy equipment dealership environment, particularly within service trucks, is not just about cleanliness or organization. It’s about building a culture of efficiency, safety, and excellence. By embracing these principles, dealerships can not only enhance their service quality but also improve customer satisfaction and the overall health of their business. Remember, 5S is more than a methodology; it’s a pathway to excellence in the heavy equipment industry.
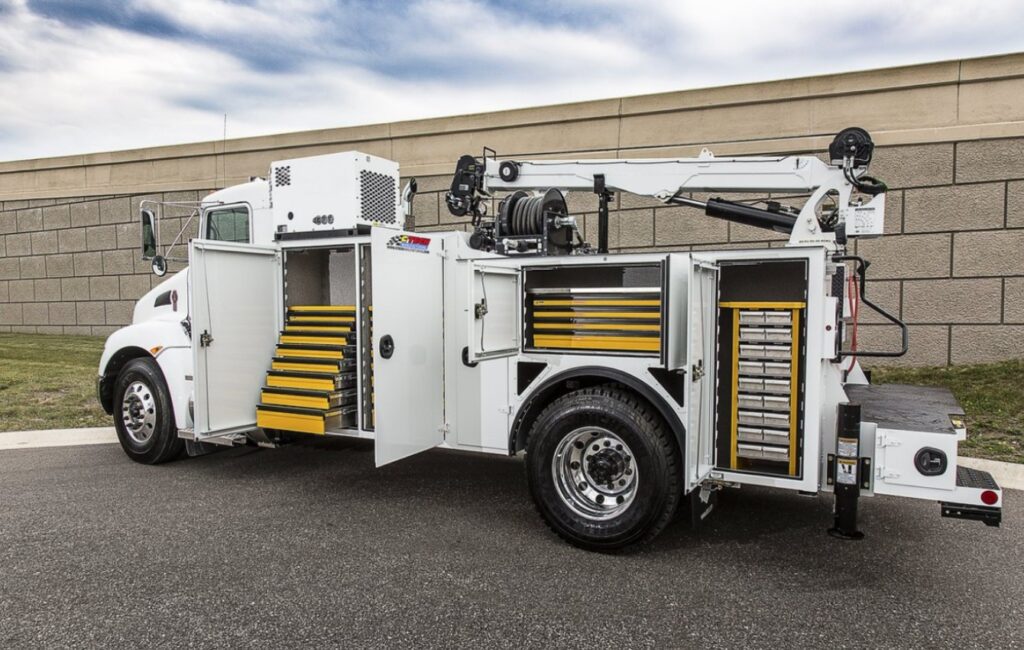